Plate and frame filter presses are used in the beverage industry, for example, to clarify intermediate products.
A suspension of diatomite and water (recommended) is prepared in a tank. A pump ensures that the solid remains suspended and does not settle. The pump delivers the suspension into the individual separating chambers of the plate and frame filter press. A separating chamber is formed by one filter frame and two filter plates. The filter plates are grooved and covered over with filter cloths. The filtrate passes through the filter cloth and flows via the grooves in the plates into a collecting pipe. The filtrate exits the plate and frame filter press through the collecting pipe and is collected in the filtrate tank. The solid material is separated off at the filter cloth, where it forms a growing filter cake. As the filter cake becomes thicker, its flow resistance also increases. When the separating chamber is full, or a maximum pressure difference has been reached, the filtration process is ended. The plates and frames of the plate and frame filter press are pulled apart. The filter cake can be removed. For the next filtration the plates and frames must be pushed back together. A spindle is used to press them together. The press forces ensure that the suspension does not leak from the contact points between the plates and the frames, but is forced through the filter cloth.
The flow rate through the plate and frame filter press is adjusted by a valve. The pressure occurring during filtration is indicated on a manometer. The filtrate tank is scaled. This means a stopwatch can be used to measure the flow rate. An included opacimeter allows the solid concentration of the filtrate to be determined. A drying chamber is recommended for evaluation of the experiments.
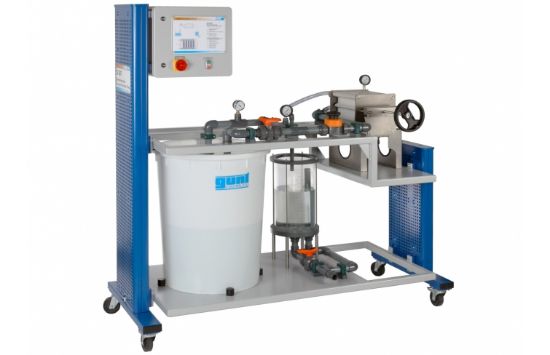