The climate in the cold storage room has a significant effect on the quality of the products stored there. This climate depends on different influences, such as the surface temperature of the evaporators, cold storage room temperature, degree of evaporator icing, quantity and type of refrigerated goods etc.
The icing of the evaporators depends on the evaporator and room temperatures and the quantitiy of humidity introduced by the refrigerated goods. Icing of the evaporators significantly reduces the refrigeration capacity and must therefore be prevented as much as possible by periodic defrosting, i.e. heating the evaporator surfaces. In addition to the periodic defrosting at set times, there is defrosting performed as required by measuring the actual ice coating. The evaporator surface can be heated from the outside by electric heating or from the inside by hot gas directly from the refrigerant compressor.
The trainer features a large refrigeration chamber. Two evaporators allow for an investigation of the effect of different evaporator sizes on the cold storage room climate and the icing. An electric defrost heater and hot gas defrosting are available. The defrost process can be performed as required using a defrost controller or at set intervals using a defrost timer.
Two adjustable heat sources in the refrigeration chamber simulate the cooling load. One of these heat sources generates water steam to simulate the introduction of humidity into the refrigeration chamber.
The measured values can be read on digital displays. At the same time, the measured values can also be transmitted directly to a PC via USB.
The data acquisition software is included. The data acquisition enables e.g. the recording of the defrosting process over time and the online representation of the climate in the refrigeration chamber in the h-x diagram. The refrigerant mass flow rate is calculated in the software from the recorded measured values.
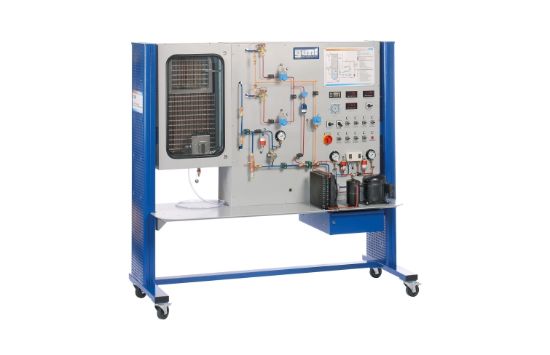